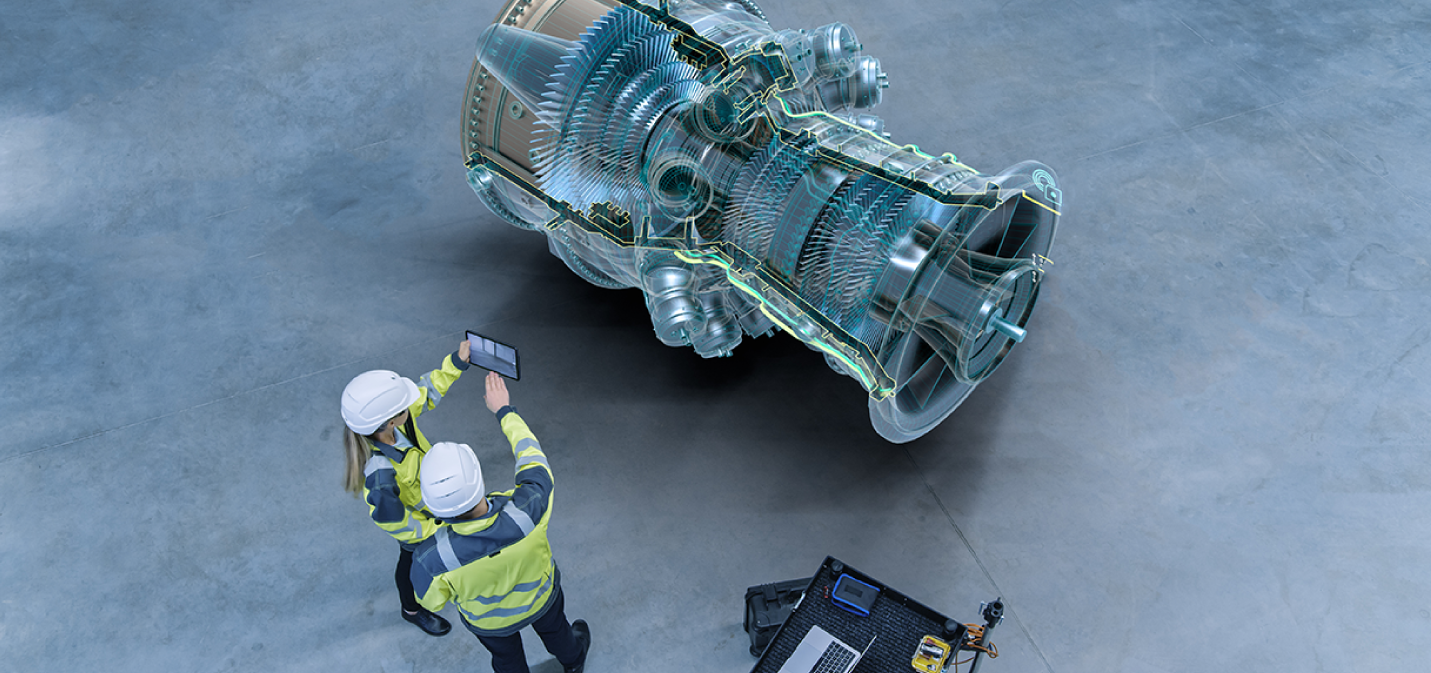
Smooth and rapid alignment between as-designed vs. as-built 3D entities
In today’s precision manufacturing environment, comparing as-designed CAD models with as-built components is critical for quality assurance. Open CASCADE BestFit SDK provides an advanced algorithmic solution for optimal alignment between point clouds from 3D scanning and their corresponding CAD models. This powerful component delivers exceptional accuracy and performance for Computer Aided Inspection applications where dimensional precision is paramount.
BestFit solves the fundamental challenge in quality control: determining exactly where and how significantly a manufactured part deviates from its digital design. By generating the optimal transformation matrix between scan data and CAD models, the algorithm enables precise deviation analysis across complex geometries.
Advanced Algorithm Process
The BestFit Algorithm processes input datasets through a sophisticated three-step approach:
- Deviation Calculation – Precisely calculates and registers the deviation of each input point from the nominal shape, supporting projection on both surfaces and wireframes
- Error Function Computation – Constructs a comprehensive error function evaluating overall deviation patterns based on individual point measurements and their dependency on transformation parameters
- Optimization Solution – Employs advanced mathematics to solve the multi-dimensional optimization problem, determining the exact transformation that minimizes global deviation
The output is a precise transformation matrix combining translation and rotation components that, when applied to the point cloud, achieves optimal alignment with the reference CAD model.
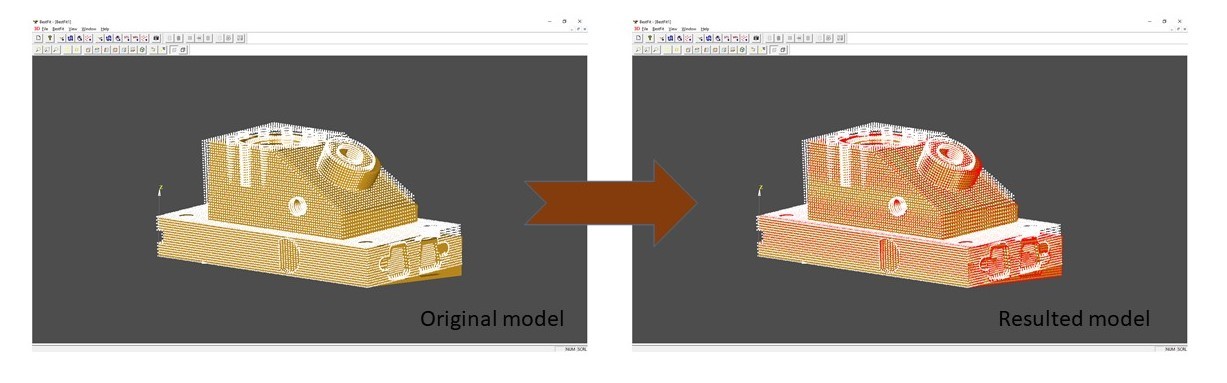
Technical Benefits
- Flexible API Integration – Convenient C++ API designed for seamless integration into existing inspection applications
- Multi-Surface Projection – Support for point projection on complex surfaces and/or wire-frames
- Optimized Performance – Highly efficient algorithms providing accurate and fast deviation computation
- License Independence – Requires no third-party licensing for deployment
- Cross-Platform Support – Available on all platforms supported by Open CASCADE Technology
Business Benefits
- On-Site Dimensional Verification – Enable real-time comparison between manufactured parts and their digital prototypes
- Accelerated Quality Control – Dramatically reduce time spent on manual alignment and inspection tasks
- Enhanced Measurement Accuracy – Improve reliability and precision of inspection results through optimal alignment
- Proactive Manufacturing Control – Diagnose and prevent manufacturing and assembly issues before they impact production
- Streamlined Metrology Workflows – Integrate scanning and inspection processes into cohesive quality control systems
Key Applications
The BestFit component delivers exceptional value across multiple industries:
- Precision manufacturing quality control and inspection
- Reverse engineering of physical components
- Part alignment verification for complex assemblies
- Dimensional metrology and certification
- Point cloud to CAD registration for digital twins
- Aerospace and automotive component verification
For detailed technical specifications and integration guidance, please refer to our comprehensive documentation included with the component.