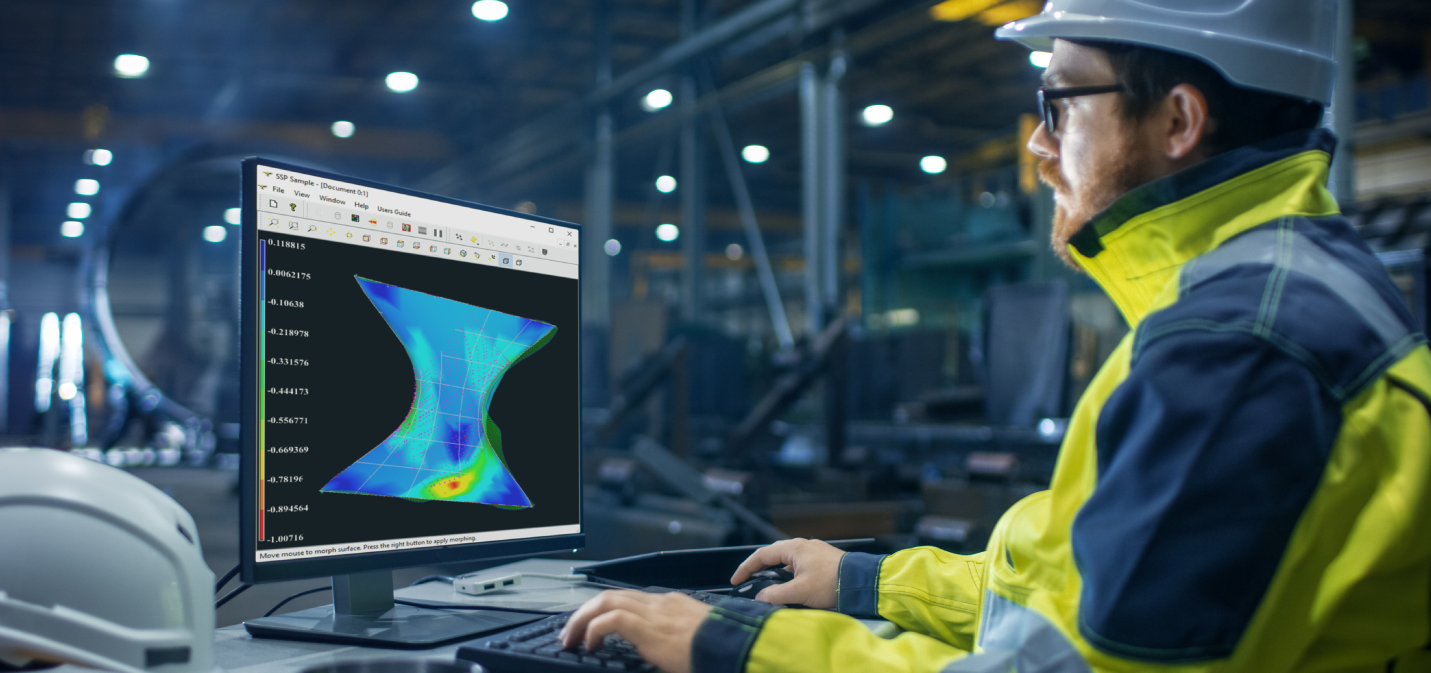
Transform Laser Scan Data into High-Quality CAD Surfaces
The trend of using laser scanning in manufacturing has seen massive proliferation in recent years across various industrial fields. However, complex parts and imperfect scanning processes often lead to significant holes in captured data and low-quality results that limit usefulness for downstream applications.
The OPEN CASCADE Surface from Scattered Points (SSP) SDK provides a powerful solution for transforming incomplete point cloud data into precise B-Spline surfaces. This specialized component delivers advanced capabilities not only for recovering missing data lost during acquisition but also for performing sophisticated operations like hole filling, surface morphing, and gaps filling between surfaces and wireframes.
Powerful Surface Reconstruction Technology
The SSP algorithm provides a comprehensive foundation to perform various operations in the field of surface reconstruction using a variational method that minimizes energy-like functionals to produce B-Spline surfaces satisfying specific input criteria.
Core Capabilities:
- Surface from Scattered Points – Construct surfaces that conform to given point, tangential, scalar, and linear constraints
- Hole Filling – Create surfaces that satisfy boundary constraints to fill gaps in models
- Surface Morphing – Modify existing surfaces to satisfy spatial constraints while preserving characteristics
- Gaps Filling – Adjust surfaces to reduce gaps between surface and wireframe elements
Surface Generation Process
The SSP algorithm follows a structured process to generate high-quality surfaces from point data:
1. Loading the Constraints
The system processes point constraints and other specialized constraints (boundary, morphing) that are translated to point constraints. Custom constraints can be configured via combinations of several other constraints.
2. Creating or Loading the Initial Surface
The algorithm can create three types of initial surfaces:
- A plane
- A patch (trapezium on 4 points)
- A conical patch (built on 6 points)
All these surfaces are internally converted to B-Spline. Users can select from these options or build custom surfaces to fit particular requirements.
3. Generating the Final Surface
The surface is modified according to constraints through an iterative process that balances adherence to input points and surface smoothness.
Customizable Parameters
The SSP algorithm provides extensive configuration options to fine-tune the surface reconstruction process:
- Smoothing coefficient – Controls the balance between point adherence and surface smoothness
- Order of continuity – Determines how patches composing the surface maintain continuity
- Number of iterations – Defines the refinement level applied after initial calculation
- Energy coefficients – Simulates energy required to bend the initial shape
- U and V degrees – Controls the surface flexibility and complexity
- Number of knots – Adjusts the level of detail in U and V directions
Industrial Applications
The SSP SDK brings the power of variational methods to solve specific 3D reconstruction tasks in OCCT-based applications across numerous industries:
- Reverse Engineering – Convert physical parts to CAD models
- Automatic Measurements – Create reference surfaces for inspection
- Rapid Prototyping – Prepare scan data for 3D printing
- Generative Shape Design – Build complex surfaces from point constraints
- Shape Customization – Modify existing designs to fit specific requirements
- Surface Quality Improvement – Enhance surfaces through morphing techniques
- Archaeological Reconstruction – Rebuild incomplete artifacts from partial scans
Business Benefits
- Enhanced Data Recovery – Salvage value from incomplete scan data
- Improved Design Flexibility – Easily modify and adapt surfaces to changing requirements
- Reduced Development Time – Accelerate the transition from physical to digital models
- Higher Quality Results – Generate mathematically precise surfaces from imperfect inputs
- Workflow Integration – Seamlessly fit within existing OCCT-based development environments