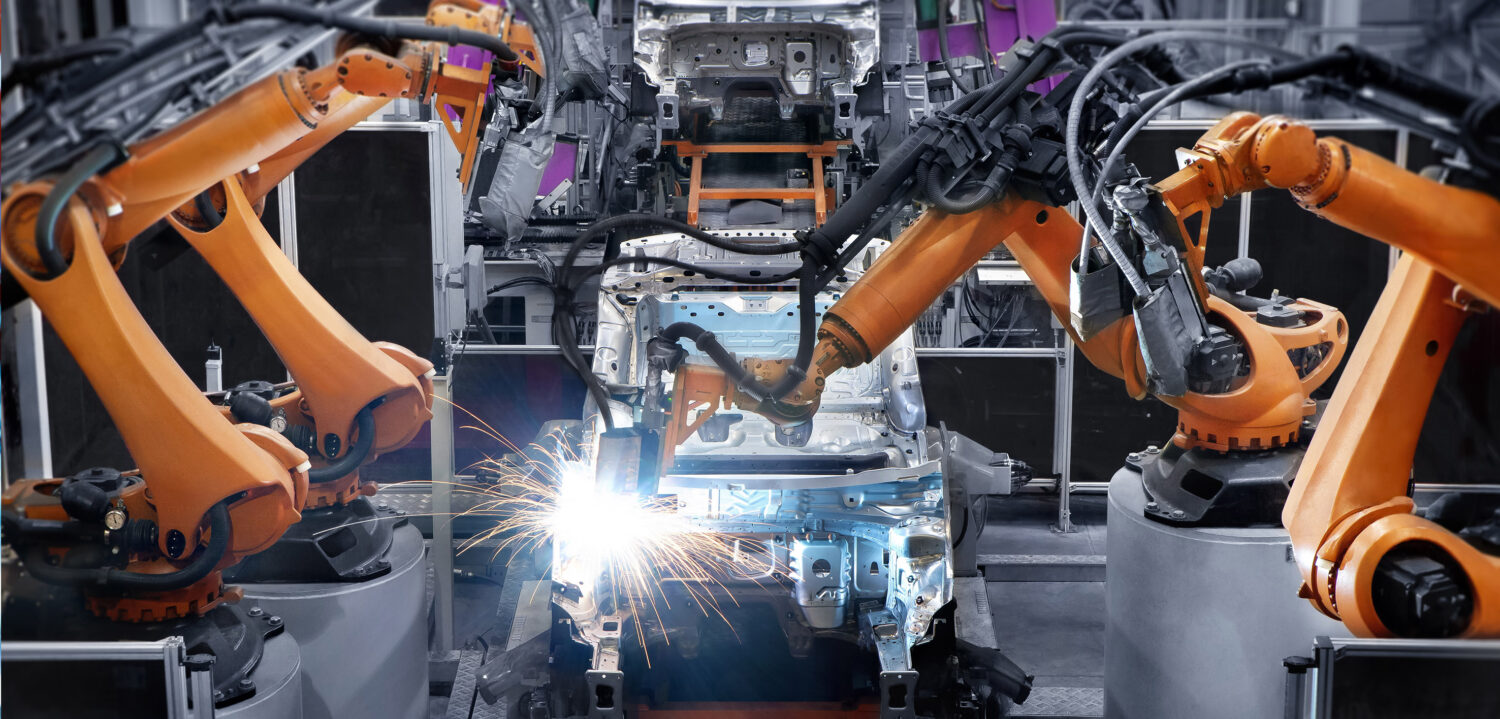
Challenge
Manufacturing simulation solutions require 3D models and the kinematics for all manufacturing equipment, robotic cells, etc. Manufacturing simulation experts normally prefer to use their favorite software solutions. Meanwhile 3D models and kinematics coming from equipment vendors is created using favorite CAD tools of a particular vendor. The gap between different representations of equipment models in different systems slows down and complicates the manufacturing simulation workflow requiring a lot of manual conversion efforts and making the process error-prone.
Solution
Open Cascade solution bridges the gap between the equipment vendors and manufacturing companies ensuring consistent and lossless data flow of the two worlds. Completeness of the transferred data is guaranteed thanks to interim Open Cascade data model compliant with ISO 10303-242 and ISO 10303-105 standards. Multiple data formats are supported. To achieve maximum automation of data flow and ensure that manufacturing simulation is always performed using the up-to-date vendor data, the solution can be integrated with all major PLM systems.
Bidirectional data link is enabled thanks to non-ambiguous mapping between manufacturing simulation endpoints and interim data model. Such an approach enables engineer’s feedback from manufacturing to equipment vendors with the purpose to modify the equipment kinematics and constraints based on manufacturing needs. The vendors and the manufacturing team are able to collaborate efficiently like this.
Business value
The end-to-end solution for manufacturing simulation workflow reduces efforts to integrate new equipment in the existing environment and in general minimizes time needed to prepare or modify manufacturing processes, for example, when launching a new factory. The equipment vendors can adopt their products rapidly to specific manufacturing needs and constraints and achieve higher level of customer satisfaction.